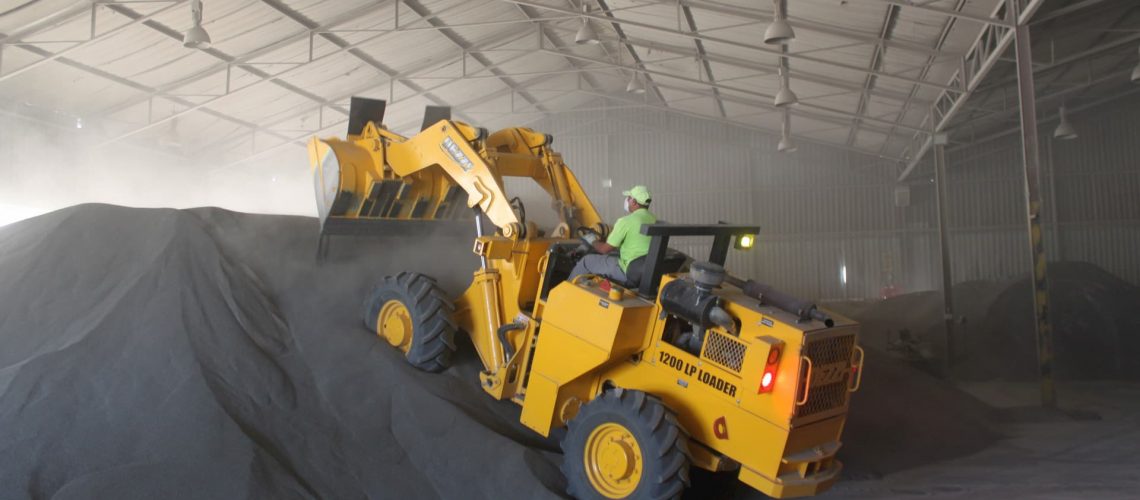
Daren
- ,
- , Machine Info
LOW PROFILE, HIGH RETURN
The Dezzi low profile loader is specifically designed for bulk handling solutions in areas where machines are restricted for height clearance. They are the ideal solution for chicken farmers, harbours, container loading and logistic industries.
OEM Dezzi and their customer Octo-Logistics have built a unique ‘partnership’ model borne out of customisation.
Based in Germiston, Octo-Logistics, whose services include bulk storage handling and bagging, falls into the five-kilometre cartage zone from City Deep Container Terminal – one of South Africa’s ‘inland ports’.
The logistics company boasts a 12 000 m² undercover warehouse, of which 7000 m² is SOS Bonded, making it ideal for cargo in transit through South Africa, be it imports or exports. In addition, the company has a 6000 m² yard for cargo utilising outside storage. Through the use of mobile ramps, they are able to load and offload containers with ease, during any weather conditions.
“Octo-Logistics was established in 2012, and we offer our clients over 70 years of collective senior experience in all elements of warehousing and logistics,” says Managing Director, Kevin Davy. “We’ve used our experience over the years to ensure that every one of our clients receives a personalised service with attention to detail in every aspect of their logistics needs – acting as an extension to all our clients’ businesses for mutual success,” he adds.
Davy, together with Warehouse Supervisor Corné Cordier, and Warehouse Manager Dudley Wilskut, collectively have a 10-year history with Desmond Equipment SA (Dezzi) products. “We’ve worked with Dezzis before – mainly the low profile 1 200 – purely because they go straight into the containers,” says Davy.
The lekker feel of local
The South African designed and manufactured Dezzi low profile loader is specifically designed for bulk handling solutions in areas where machines are restricted for height clearance. They are the ideal solution for chicken farmers, harbours, container loading and logistic industries.
“When we started Octo-Logistics in 2012, we found ourselves getting into bulk cargoes with a new client. We bought our first Dezzi about 6 months into the contract, and it has just saved us,” explains Davy. “The Dezzi 1200 has offered so much flexibility: we use it to bag cargo, to load tippers, we load containers with it – there are a whole lot of applications that we use it for. Typically, the warehouse setting is fairly limiting in terms of manoeuvrability, and initially our challenge was, how do we load bulk product into containers? So, we built a conveyor belt with a big hopper. The containers reverse up to it, and we just load the bulk directly into the container,” explains Davy.
The loader does very well in these applications, where normally a conventional skidsteer would be used. “The Dezzi low profile is fitted with a 0.9m³ bucket, so with every scoop, you’re getting tripple the loading than you would with a large skidsteer,” says Carl Gutzeit, Managing Director, Dezzi Equipment.
“The cost of the Dezzi, versus hiring another machine saved us over R10 000 per month, and at the same time doubled our loading capacity. At our top warehouse facility on a good day with the Dezzi, we can load 25 containers on the conveyor system,” says Davy. “We are able to load 34 tonnes in half an hour into a tipper truck – that’s where the 1 200’s big bucket comes into play,” he adds.
Versatility
“Then we took on small parcels of chrome. For this application, we needed to go into the container. We have mobile ramps to offload containers. The Dezzi, with a bucket-load of chrome goes straight up that ramp, at an approximately 15° angle, straight into the container and tips it,” says Davy. “The low-profile was designed for applications where height restrictions are an issue for machines with a full cab,” adds Gutzeit.
But with the harsher application, came a new challenge. “The bolt-on cutting edges on the bucket were wearing, because the application is like sandpaper and the bulk density is heavy – this was eating through the cutting edge. Gutzeit solved the problem by re-designing, through sourcing a stronger metal, a new and stronger cutting edge for us,” says Davy.
Cordier elaborates: “Generally, we get around 800 hours on a cutting edge, even with a hard application. But with the very course, bulk-dense application, we were getting around 350 – 400 hours. The new cutting edge solves that.”
Expanding on investment
As a clear testament to customer satisfaction, Octo-Logistics bought their second machine about 6 months ago – when the older machine was 3 years old. “The older machine has almost 4 000 hours on it. This is quite a lot for a three-year-old machine, but keep in mind that it starts at 07h30, and some nights only switches off at midnight – which is an 18-hour shift for the machine,” stresses Cordier.
Davy adds, “We would never have bought a Dezzi if we didn’t think it would do what we needed. Keep in mind, we’re a small company – an over one-million rand purchase is a big deal for us. And for us, investing in Dezzi twice, says something. The second machine is used for other warehouse operations. Our contract renewal with our client is coming up shortly, and the client has asked for reassurance in terms of capability, and we are able to provide it because of our second Dezzi purchase as backup.”
Customisation
A major benefit of Dezzi being a South African manufacturer is that clients can visit the factory in Port Shepstone, and discuss any customisations with the Dezzi engineers to suit their specific application.
Davy says that Octo-Logistics is very happy with Dezzi’s flexibility and the ability to adapt the machine to their needs. “We paid the factory a visit before purchasing our second Dezzi, and went through the process of identifying and discussing our needs to suit our specific applications, and Dezzi customised all of this for us. This included the new cutting edges. Another example is the pins on the bucket were being compromised by dust, this was resolved through innovative thinking from Dezzi,” says Davy.
“As a small company investing in two machines, we wanted to do our homework. At the factory, we went through the production process, we wanted to know every part of the process; starting with production on a machine, spray painting, where the parts come from, until the machine rolls off the assembly line. That way, when we’re back on site, if anything goes wrong, we at least have an idea. But Dezzi is always just a phone call away,” enthuses Davy.
Training
“When we bought our first machine, Dezzi was on site to train our operators. They went through a training programme – how to do a check-list; what to check in the morning, what to check at lunchtime – water, oil, greasing, how to operate, what not to do in terms of abuse on the machine,” says Davy.
This kind of ‘day-to-day maintenance’ goes a long way. “We have to give credit to Octo-Logistics for maintaining their own machine and looking after it, making sure their operators do their checks in the morning,” says Gutzeit.
After-sales service
Davy says their Dezzi is a strong machine and they haven’t had any major issues with it. “We have the Dezzi service technician, Marcel Snyman, he is based at Dezzi’s Johannesburg branch in Sebenza, Edenvale. Dezzi are always quick to send a mechanic around whenever we need one.”
“But we look after the machine and conduct routine maintenance on site – we keep it clean, check the filters, grease the pins every day. Especially with the type of product we handle we have to look after the pins and bushes,” adds Cordier.
Dezzi Sebenza has a full workshop – parts, stock-holding, service technicians – services are done on site, or for major services, the machine is booked into the workshop.
Davy concludes that another major attraction to Dezzi is that there’s no electronics. The drivetrain is simple; it’s an engine with hydraulics. Fitted with a JCB 444 turbo engine, which offers 75kW at 2 400rpm, the 7,1t loader is known for its simplicity of the drivetrain and carries a one year, 2000-hour warranty, except for the sturdy chassis which carries a 5 000-hour warranty. Extended drive train warranties are available.
So, it’s with Dezzi’s simplicity, customisation and ‘built Africa tough’ approach that Octo-Logistics are able to increase productivity for higher return.
About Desmond Equipment SA
The Desmond Group of companies has been in business since 1973, and are renowned in the last 24 years, for the manufacturing of South African designed Dezzi equipment; the first front-end loader rolled off the assembly line in 1996.
Desmond Equipment SA’s head office and factory is based in Port Shepstone, and aftermarket service is offered nationwide in southern Africa into sub-Saharan Africa with strategically placed branches and dealers.
The machines manufactured at Dezzi’s Port Shepstone factory include:
- Articulated dump trucks
- Articulated haulers
- Rigid hauler tractors
- Front-end loaders
- Skidders
- Cane loaders
- Motor grader (7,5t)
- Three-wheel loggers
These machines and various customised earthmoving equipment are earmarked for the cane, forestry, sugar, plant hire, construction, building, mining and quarrying industries.
The company recently signed an agreement with Merchant West and is able to offer competitive tailor-made financial solutions to existing and new customers.
For more information, please feel free to contact us below.
Contact Us
Dezzi Machine Sales
Phone: 039 685 4100
Email: info@dezzi.co.za
Dezzi Raceway
Phone: 084 952 1973
Email: raceway@dezzi.co.za